Course Catalog
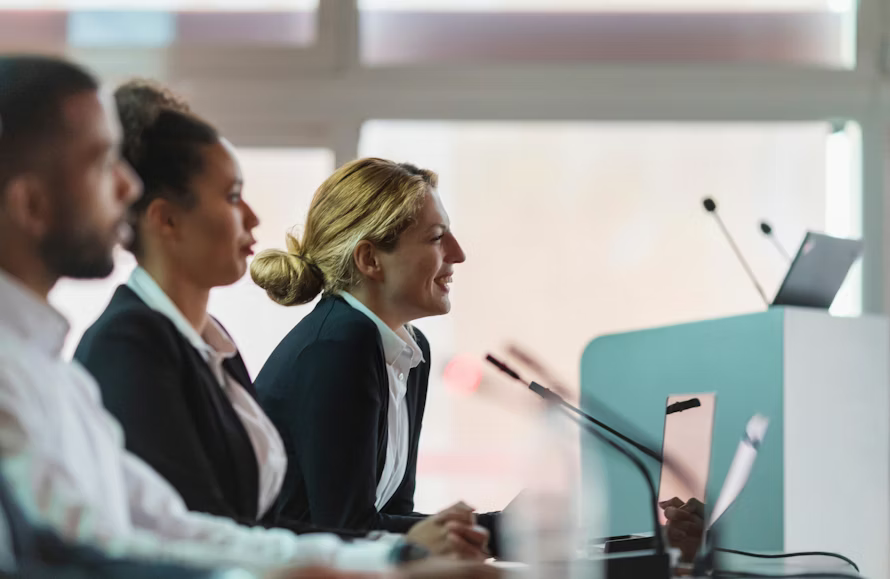
A lockout/tagout procedure should include the following six steps: Preparation Shutdown Isolation Lockout/Tagout Stored Energy Check Isolation Verification Let's take a closer look at the steps for lockout/tagout safety. Step 1: Preparation The first step of locking and tagging out equipment for service and maintenance is to prepare. During the preparation phase, the authorized employee must investigate and gain a complete understanding of all types of hazardous energy that might be controlled. In addition, it's important to identify the specific hazards and of course means for controlling that energy. Step 2: Shut Down With planning complete, the actual process of powering down and locking out machines begins. At this point, it's time to shut down the machine or equipment that will be serviced or maintained. Another important part of this step is to inform any employee affected by the shutdown, even if they won't play a role in the service or maintenance. Step 3: Isolation The next step of the lockout/tagout procedure is to isolate the machine or equipment from any source of energy. This may mean any number of things, such as turning off the power at a breaker or shutting a valve. Step 4: Lockout/Tagout With the machine or equipment isolated from its energy source the next step of lockout/tagout is to actually lock and tag out the machine. During this step, the authorized employee will attach lockout and/or tagout devices to each energy-isolating device. The point is to apply the lockout mechanism on the energy-isolating device in a way so it stays in the "safe" position and cannot be moved to the unsafe position except by the person performing the lockout. Tagout refers to applying a tag on the device as well. This tag includes the name of the person who performed the lockout and additional information. Step 5: Stored Energy Check Even after the energy source has been disconnected and the machine has been locked out, that doesn't entirely guarantee that there's no hazardous energy still stored within the machine or that it's even safe to perform the maintenance. At this time, it's important to look for any hazardous energy thats been "stored" within the machine, or any "residual" energy. During this phase, any potentially hazardous stored or residual energy must be relieved, disconnected, restrained, or made non-hazardous in some other way. Step 6: Isolation Verification This last step is all about making sure. Yes, you've shutdown the machines, isolated them from their source of power, locked them out, and checked for hazardous stored energy. But now's the time to double-check that you did it right and it's now safe to work on the machine or equipment. At this point, an authorized employee verifies the machine has been properly isolated and de-energized.
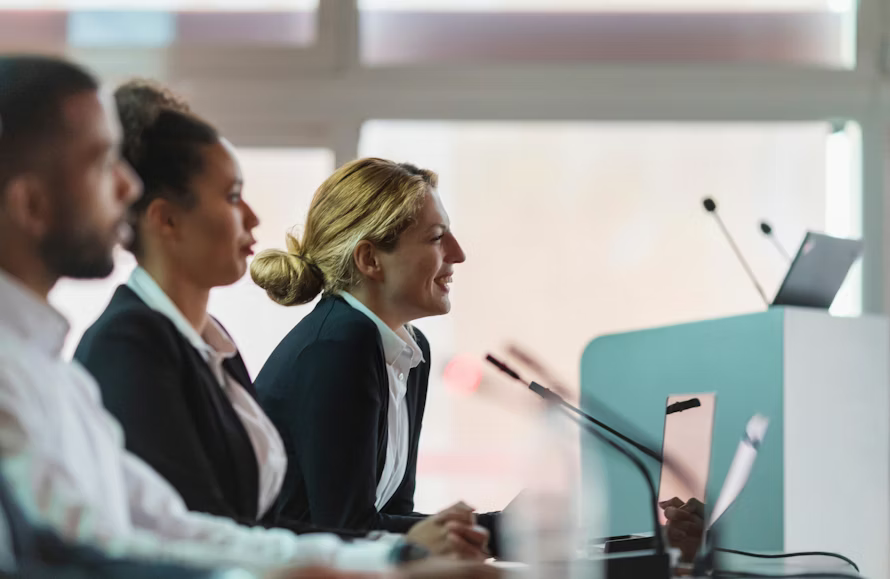
A lockout/tagout procedure should include the following six steps: Preparation Shutdown Isolation Lockout/Tagout Stored Energy Check Isolation Verification Let's take a closer look at the steps for lockout/tagout safety. Step 1: Preparation The first step of locking and tagging out equipment for service and maintenance is to prepare. During the preparation phase, the authorized employee must investigate and gain a complete understanding of all types of hazardous energy that might be controlled. In addition, it's important to identify the specific hazards and of course means for controlling that energy. Step 2: Shut Down With planning complete, the actual process of powering down and locking out machines begins. At this point, it's time to shut down the machine or equipment that will be serviced or maintained. Another important part of this step is to inform any employee affected by the shutdown, even if they won't play a role in the service or maintenance. Step 3: Isolation The next step of the lockout/tagout procedure is to isolate the machine or equipment from any source of energy. This may mean any number of things, such as turning off the power at a breaker or shutting a valve. Step 4: Lockout/Tagout With the machine or equipment isolated from its energy source the next step of lockout/tagout is to actually lock and tag out the machine. During this step, the authorized employee will attach lockout and/or tagout devices to each energy-isolating device. The point is to apply the lockout mechanism on the energy-isolating device in a way so it stays in the "safe" position and cannot be moved to the unsafe position except by the person performing the lockout. Tagout refers to applying a tag on the device as well. This tag includes the name of the person who performed the lockout and additional information. Step 5: Stored Energy Check Even after the energy source has been disconnected and the machine has been locked out, that doesn't entirely guarantee that there's no hazardous energy still stored within the machine or that it's even safe to perform the maintenance. At this time, it's important to look for any hazardous energy thats been "stored" within the machine, or any "residual" energy. During this phase, any potentially hazardous stored or residual energy must be relieved, disconnected, restrained, or made non-hazardous in some other way. Step 6: Isolation Verification This last step is all about making sure. Yes, you've shutdown the machines, isolated them from their source of power, locked them out, and checked for hazardous stored energy. But now's the time to double-check that you did it right and it's now safe to work on the machine or equipment. At this point, an authorized employee verifies the machine has been properly isolated and de-energized.
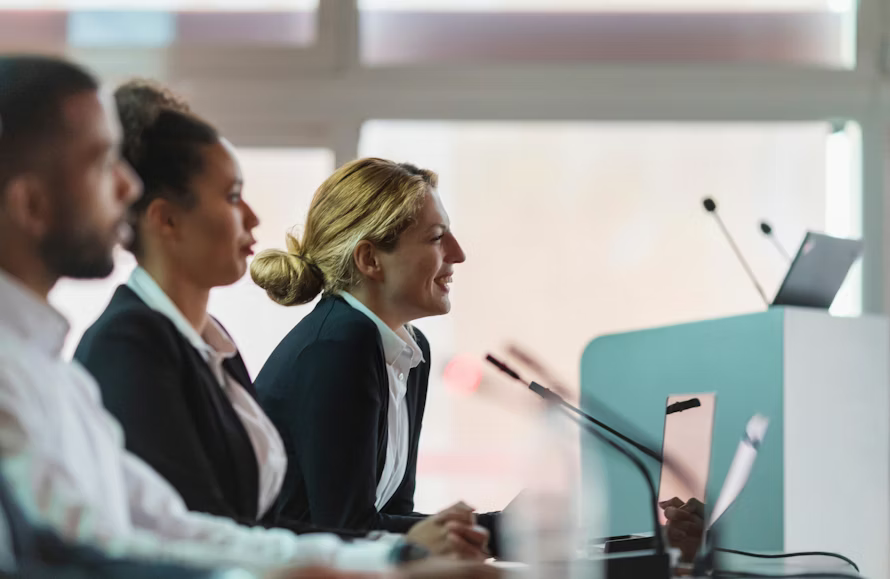
The decisions that your employees make will literally define your organization. Make sure that when your employees are confronted with difficult legal and ethical challenges they have the training to make the right decision every time. Ethics Made Simple is a short but comprehensive workplace ethics training program that covers virtually every major workplace ethics topic. This business ethics training course covers: Stealing workplace resources such as office supplies, unauthorized photocopies, and computer printouts. The theft of merchandise from retail locations or manufacturing facilities. Illegally copying or downloading patented or copyrighted materials Taking credit for or stealing the work of co-workers and passing it off as your own or taking full credit for a project you were given assistance on. Reporting more hours than you actually worked, falsifying pay records or reporting inflated business expenses for reimbursement. Deliberately doing less work than you are capable of out of laziness or to lower future expectations. Socializing with friends or family during work hours via the telephone, social networking sites, instant messaging or any other means of communication. Falsifying company documents to pass inspections by your organization or by local, state or federal government officials. Lying to or misleading customers about the attributes of your organization’s products or services or the ability to deliver those products and services. Falsifying the results of research and development to benefit your organization or to further your own personal career. Over-promising results in order to gain support for a project or for personal advancement within an organization. Destroying sensitive company documents and emails that could be harmful in the case of audits, reviews, and litigation. Violating anti-trust laws by colluding with competitors. Manipulating financial information to achieve organizational or personal goals Failing to follow your organization’s safety procedures or failing to follow federal, state or local government safety rules. Viewing or sharing confidential customer, patient or employee information without authorization or approval. Insider trading Gossiping or spreading rumors about your co-workers. Verbally intimidating a co-worker through the use of taunting, teasing, yelling and sarcasm Menacing a co-worker with threatening looks, gestures and body language. Sexual Harassment Giving bribes to or accepting bribes from a business competitor for confidential information. Giving bribes or gifts to public officials for favorable rulings on inspections, licenses, permits or other government controlled decisions. Bribing public officials from foreign countries. Basing an employment decision such as hiring, promotion or compensation on a person’s race, color, national origin, age, gender, marital or family status, religion or genetics rather than on his or her ability or experience. Treating a co-worker poorly or unfairly because of a bias, stereotype or prejudice stemming from a perceived difference. The consequences of violating ethical standards This unique course breaks workplace ethics down into digestible bites by covering all the issues that you want your employees to recognize as unethical and possibly illegal. Once your staff has seen this video and passed the quiz, you will have confidence that they will recognize unethical conduct when they see it...and avoid it!
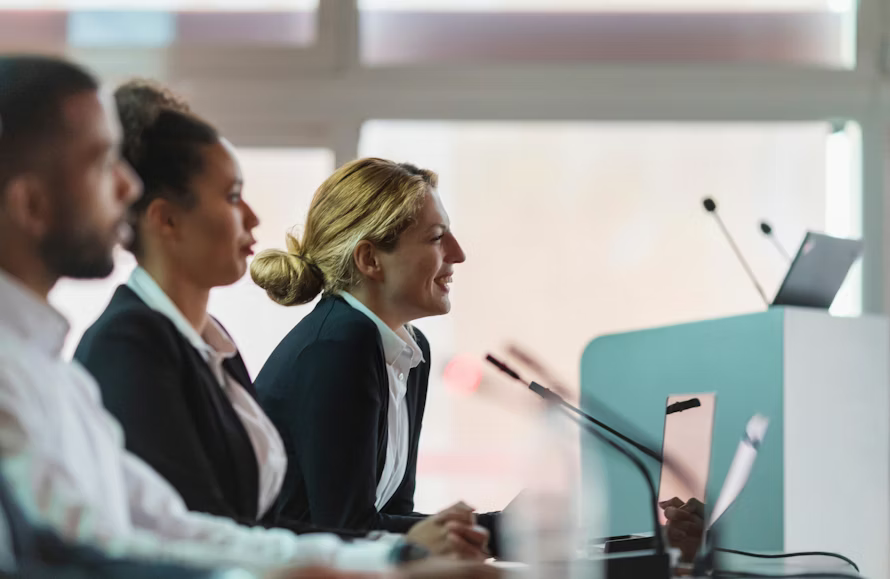
Abusive Conduct in the Workplace: California AB2053 Training
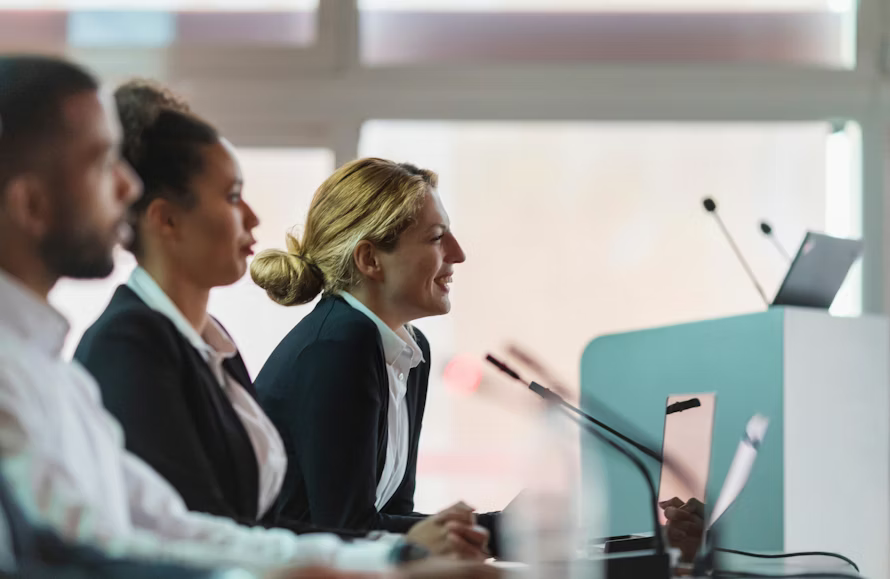
Abuso de Sustancias en el Lugar de Trabajo: Capacitación Sobre Drogas y Alcohol
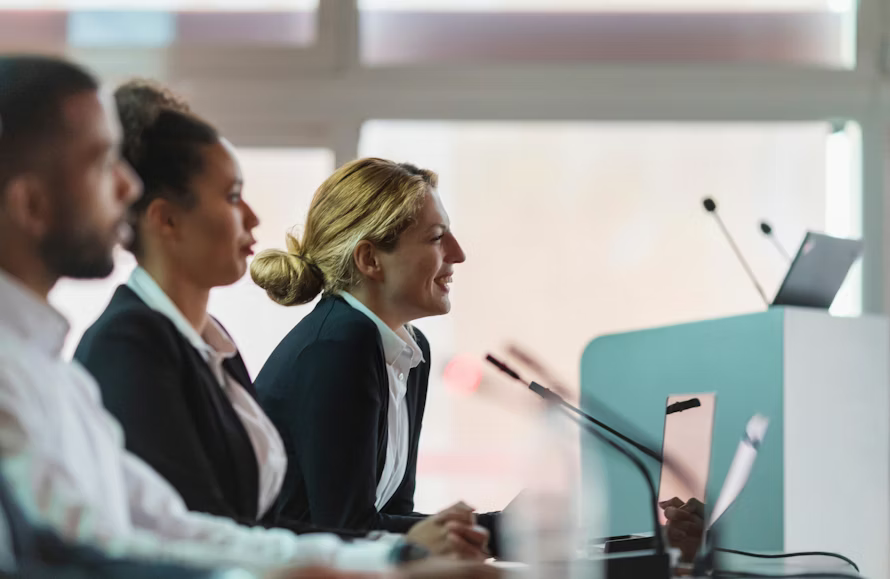
Accident Causes and Prevention (Janitorial)
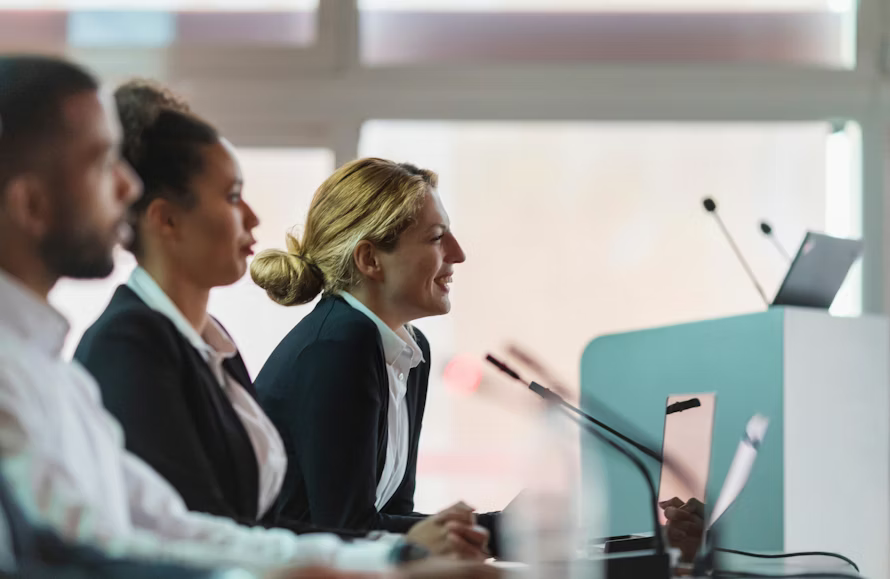
Accident Investigation (short refresher)
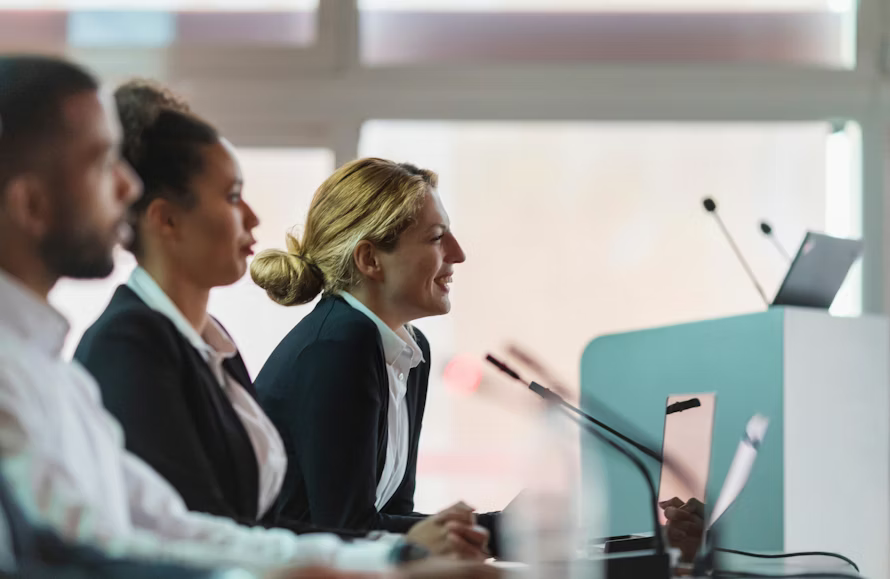
Overview This course, developed in conjunction with the experts at the U.S. Department of Transportation's (DOT) Transportation Safety Institute (TSI), covers the Accident Preventability Evaluations portion of the Federal Motor Carrier Safety Administration (FMCSA) Accident Countermeasures Manual. Reduced accident rates translate into lower insurance costs, less lost time by drivers, lower repair costs, and safer highways for everyone. Establishing and employing a company standard for safe driving will help reduce accident rates.*Flash player may be required to play this course DISCLAIMER: this course does not track/score like other interactive courses. If you require one that does, please reach out to your representative.
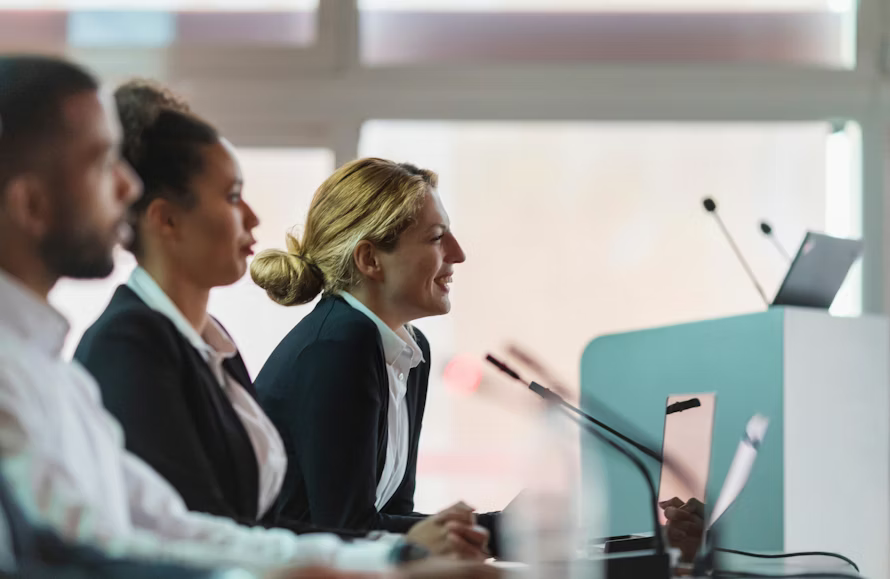
Accident Reporting - Supervisor's Guide
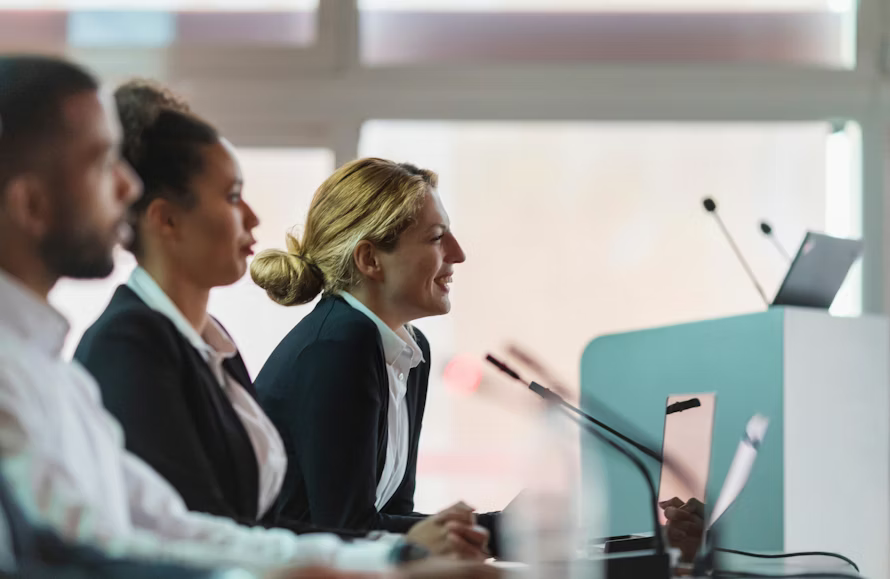
Acoso en California: Los grupos protegidos
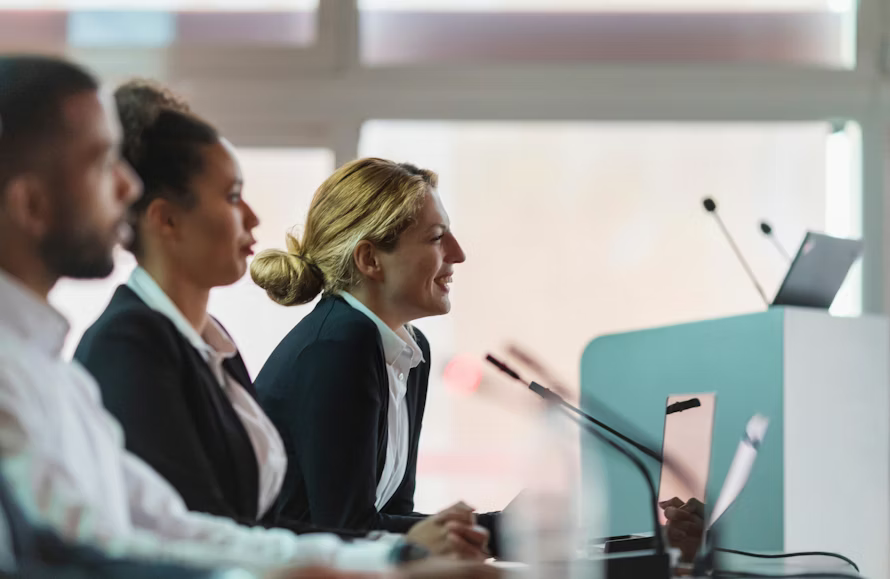
Acoso sexual en California para gerentes y supervisores (AB1825) Curso de 2 horas
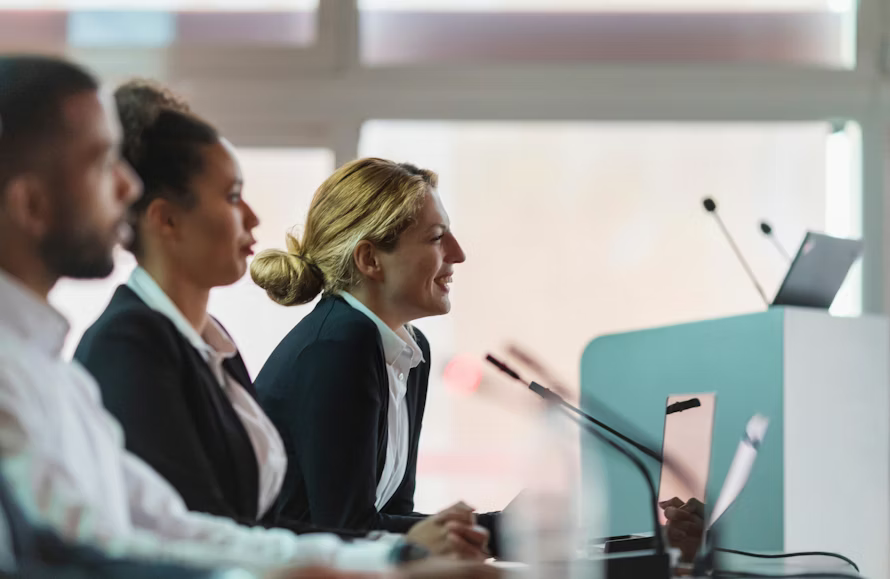
Acoso sexual en Connecticut Curso de 2 horas para no supervisores
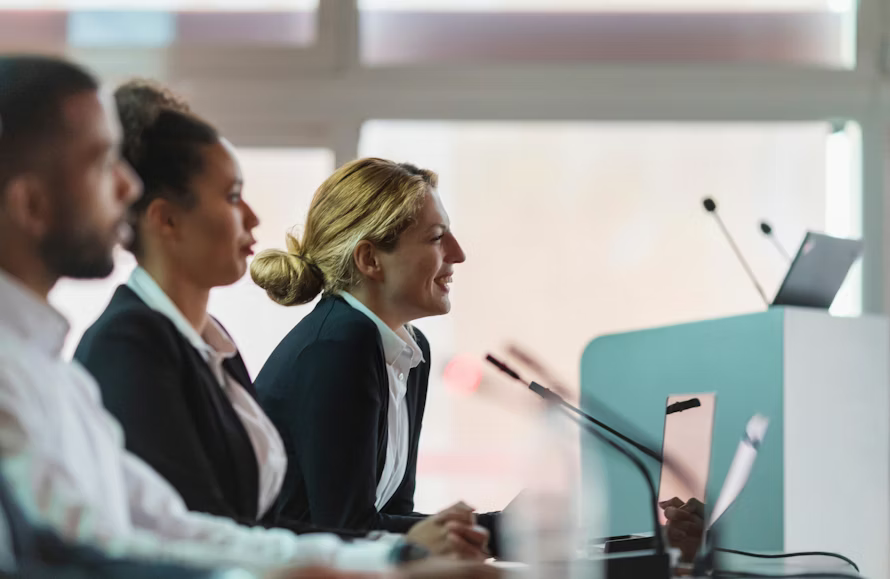
Acoso Sexual: Investigación de Denuncias
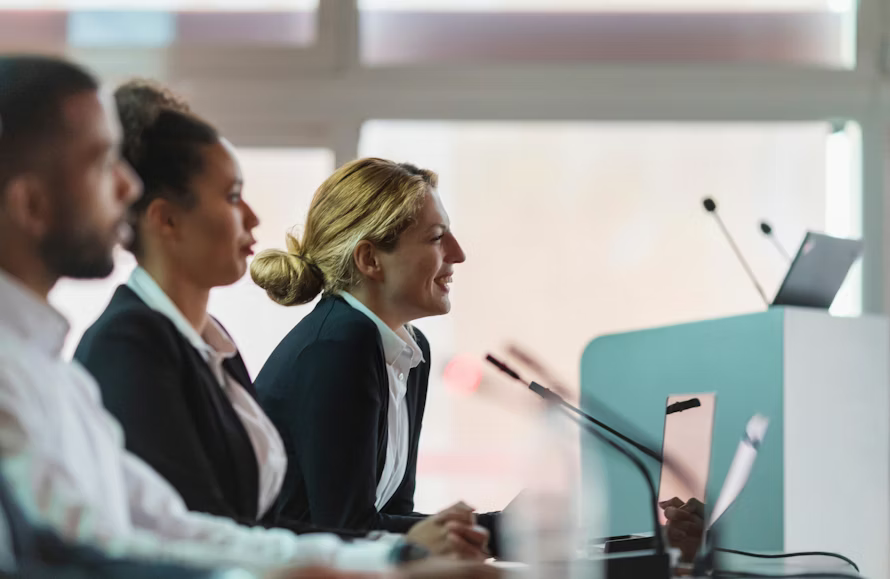
Acoso sexual no supervisado de 1 hora en California
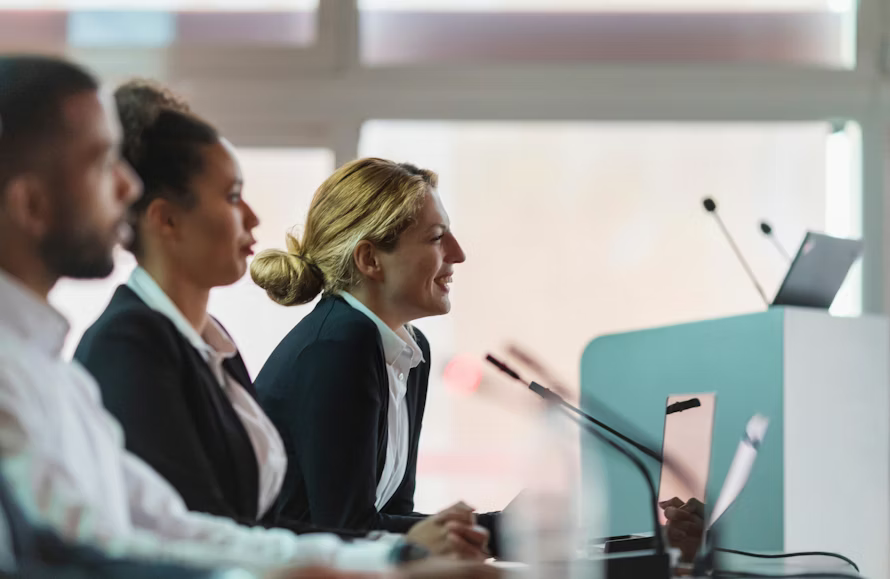
Go work in an office, they said. It'll be safe, they said. Sure. Hazards face everyone, in every environment. This training package focuses on the top hazards facing office workers: hazard awareness, accident prevention, and how to respond in case of an emergency or other incident. These can range from basic ergonomic hazards, to violence in the workplace, to responding to natural disasters. The diversity of dangers and health and safety considerations in office settings is vast.Employees taking this course will run the whole gambit. We start off with one of our most sought-after topics: active shooters in the workplace. Then we throttle back to focus on the workplace culture. This includes topics such as bullying, setting and enforcing healthy boundaries, drug and alcohol abuse, and even how to work on communication skills aimed at conflict resolution and deescalation techniques. This segues into the ever-important trainings on workplace harassment - also honing in, specifically, on sexual harassment training for employees.And what about the other hazards and incident response skills you need in office settings? This training package will prepare office employees to respond to fires (and our training isn't just aimed at anyone - we specifically look at fire hazards and response in office settings). To go along with fire prevention, employees will be trained in the use of fire extinguishers. We'll also cover responding to more than just fires. In the event of injury, everyone needs to know how to respond. That's why this training includes a first aid preparation and response course. And don't forget the larger scale dangers - we also prepare your team for crisis management and emergency planning.Don't let your office team go unprepared! Build awareness, confidence, and competence by enrolling everyone in this package, today.
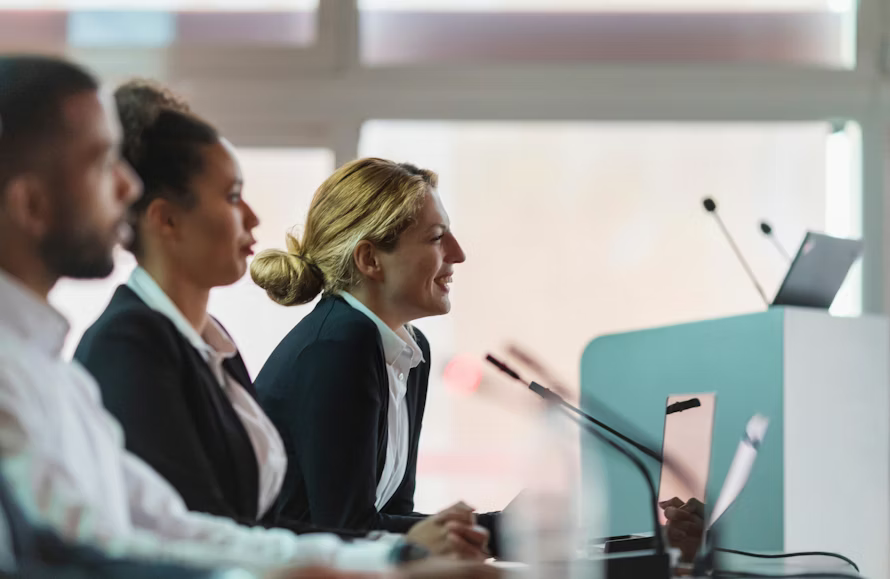
Active Shooter: In The Workplace - English Course with Multi-Language CC's
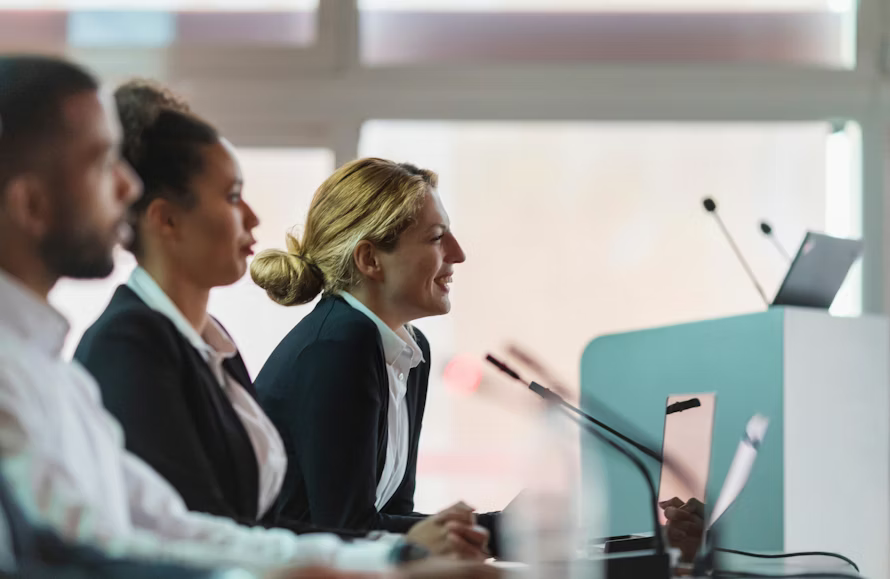
Active Shooter: In The Workplace Spanish
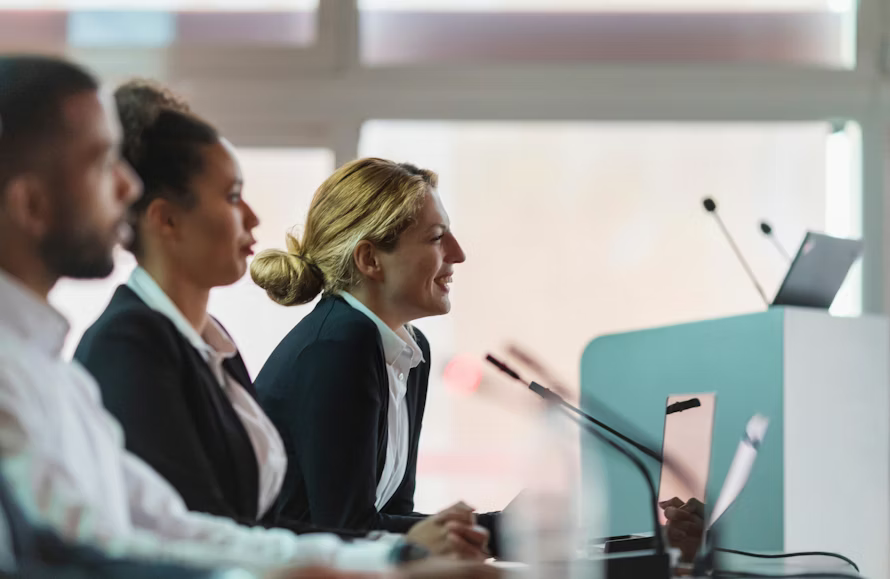
Adult/Child and Infant CPR and AED Details This program provides information on the skills and techniques to save lives. This is a review on adult, child and infant CPR and obstructed airway. AED equipment will be shown how and when to use. Runtime: 32 Min.